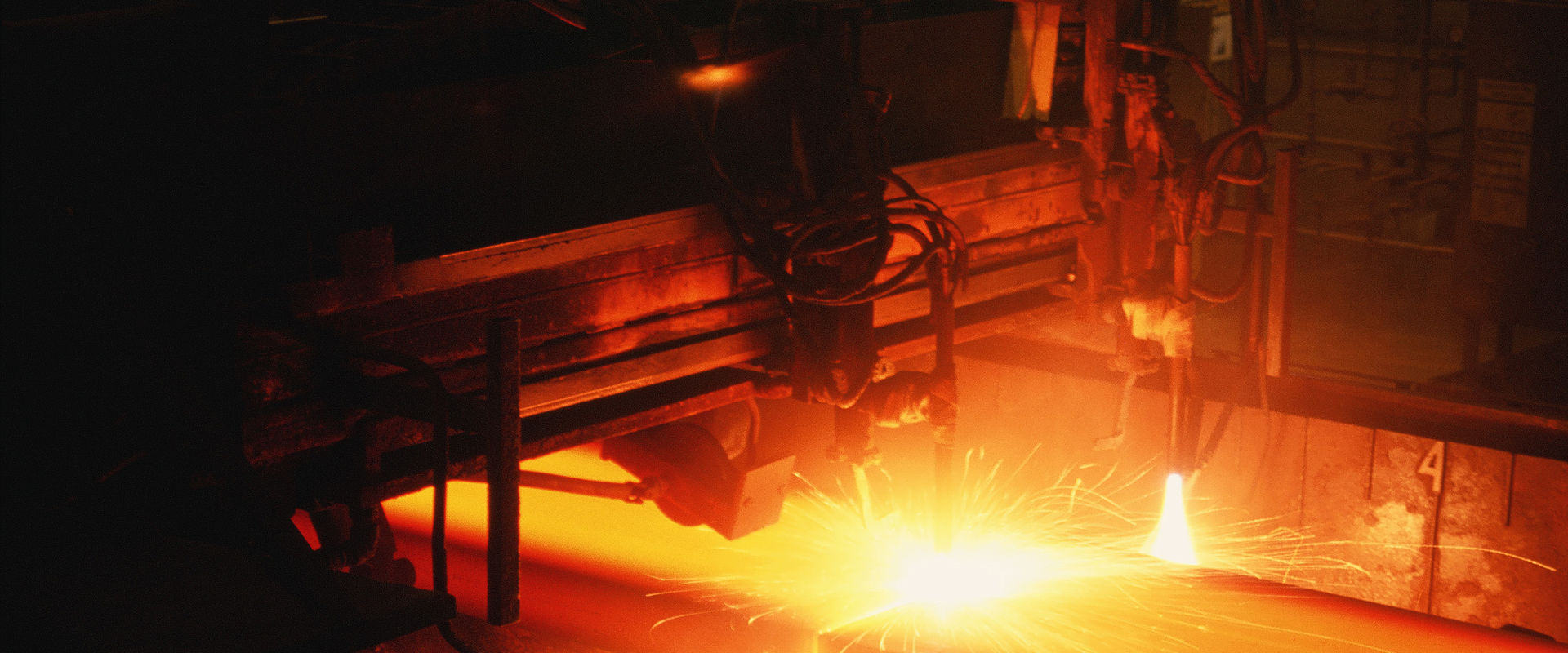
Better heat-treatment process control
Challenge
Europe’s manufacturers face the challenge of producing consistent, high-quality products using high-temperature heat treatments. Laser hardening is a surface strengthening process in which a laser heats a small area of a component’s surface to high temperatures just below the melting point to create a hard and wear-resistant finish that significantly improves the part’s in-service life span.
Precise temperatures are required to achieve the most effective hardening and are measured via non-contact temperature sensors. Over time the line of sight to the sensor becomes progressively contaminated affecting the sensors ability to measure and control temperature accurately. Typically, deterioration in the treated component’s quality has been the only indicator of temperature drift, as well as the only indicator available to adjust the process back to the required temperature. This off-line inspection leads to both wasted material and process downtime. Until recently, there were no practical devices or methods available to calibrate and correct the high-temperature sensors in-situ to ensure the laser-hardening process remained optimal over long periods of time.
Solution
The EMRP project High temperature metrology for industrial applications (>1000 °C) developed a portable ‘high-temperature fixed-point’ calibration device validated for the temperature range 1000–1400 °C for direct use in industrial settings. Such high temperature fixed points, with very reliable melting points above 1100 °C, have only become available for industrial use through the work of this project. The project developed the device and demonstrated the feasibility of using it to calibrate temperature sensors in an industrial laser-hardening system.
Impact
The portable fixed-point calibration device was tested at the German industrial research centre Fraunhofer IWS, Dresden, and its spin-out company ALOtec Dresden GmbH, which provides laser-hardening services.
This industrial testing revealed that the device could both identify and correct for large deviations from the ideal processing temperature. This confirmed its suitability for calibrating and correcting installed thermometers in laser-hardening processes, where a deviation of more than 10 °C above or below the required temperature can cause faulty parts. As a result ALOtec has been able to optimise performance of its laser-hardening process providing an improved service to its customers in the machine building, automotive and power generation sectors.
In addition, a major European engine component manufacturer is interested in a miniaturised version of the calibration device for installation in an automotive camshaft production facility. The plant is due to undergo a major improvement to its laserhardening equipment including the replacement of the process thermometers. Being able to calibrate the thermometers and therefore assess temperature accurately will vastly improve the commissioning procedure for the new laser-hardening equipment. The alternative is a trial-and-error approach where the temperature of the hardening process is adjusted until the quality of the output meets specification. This not only takes time but results in faulty camshafts until the correct output is achieved. The plant produces 100,000 camshafts per year for major automotive manufacturers, so speeding up the commissioning procedure will reduce production downtime and material waste and minimise the impact on the company’s, and its customer’s business.
- Category
- EMRP,
- Industry,