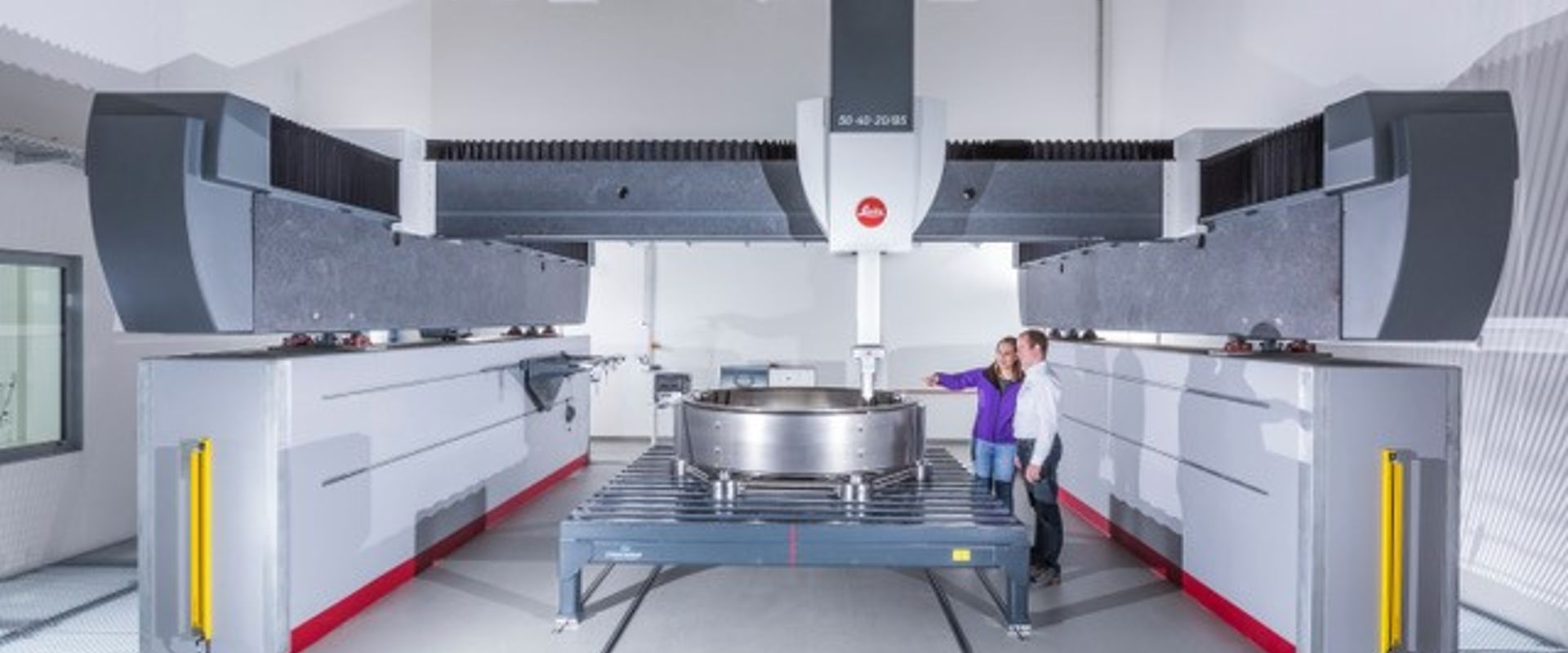
Improving wind turbine reliability
Challenge
Although the EU is on course to meet its renewable energy directive 2020 target of 20 % of its total energy consumption to be sourced from renewable sources, expansion in generation capacity must continue to reach the equivalent 2030 target of 32 %.
Electricity generation by wind energy systems (WES) has increased by 350 % over the last ten years, but few wind turbines reach the desired lifetime of 20 years without two or more failures of major drivetrain components. The resulting downtimes last days or even weeks, reducing income and adding significant maintenance costs, particularly for offshore installations.
Wind energy systems are large to optimise energy output. Transferring power effectively between turbine blades and generator, requires WES drivetrains (bearings, shafts and gears) to be correspondingly large. In these highly-stressed conditions surface irregularities cause reduced lifetimes, as, in modern steels, failures tend to be initiated at the surface. However, manufacturers lacked processes for producing these components to consistently high standards.
To ensure sufficient quality, coordinate measuring machines (CMMs) are used to measure these components. However, environmental conditions, such as variations in temperature that influence acclimatisation times, can affect measurements. Also written standards didn’t address some crucial factors, limiting inspection quality and reducing trust among users of these highvalue devices.
Solution
The EMRP project Traceable measurement of drivetrain components for renewable energy systems improved drivetrain component reliability by developing measurement standards and procedures that provided traceability to SI units. This was achieved by enabling reliable estimations of measurement uncertainty.
The developed measurement standards were optimised for industrial use, to calibrate gear size, form, and surface irregularity parameters of large drivetrain components.
Virtual measuring processes were developed to traceably measure large drivetrain components, to minimise measurement errors. Numerical simulations and practical experiments to overcome environmental effects were also performed to produce recommendations for improved CMM scanning parameters.
New algorithms developed for incorporation in CMM control software were made available to suppliers. Guidance, including on thermalisation times of large gear and large ring measurement standards, was published in six Good Practice Guides.
Impact
Hexagon Manufacturing Intelligence, the leading metrology and manufacturing solutions provider based in Wetzlar, Germany, considers its Leitz CMMs the most accurate products in the CMM market. Maintaining that lead was a significant motivator for participating in the project.
As a result, Hexagon enhanced its gear evaluation software and gear evaluation plots to offer higher quality inspections and more reliable results. A developed algorithm was incorporated into its QUINDOS Gear software and made available to all of its customers.
Users previously experienced challenging thermal drift effects, that reduced measurement reproducibility. The Good Practice Guides proved helpful for guiding Hexagon’s customers and potential customers by providing reassurance in instrument performance as well as improved inspection quality.
Hexagon was told that about half of its 2019 sales of large Leitz Gantry CMMs were positively influenced by its involvement in the project.
Ultimately, traceable measurements will lead to improved quality and reliability of manufactured WES components. This will enable higher returns on investment from wind energy systems, support expansion of this type of zero-carbon electricity production and help EU states meet renewable energy commitments.
- Category
- EMRP,
- Energy,