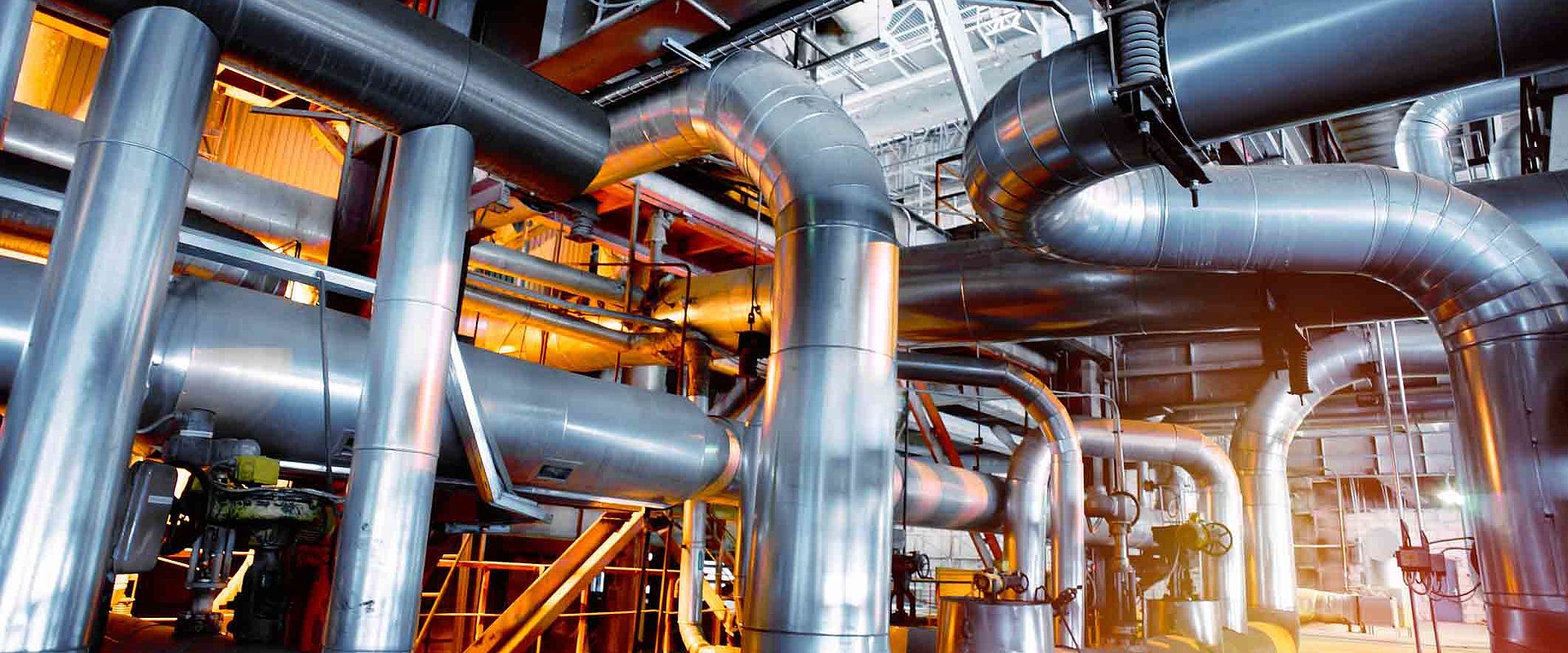
Installed sensing for power plant
Challenge
Power plant operators must reliably monitor structural integrity to ensure safety. For example, high pressure, high temperature steam can degrade and corrode the pipes that carry it. If these crack during operation, the damage and lost power generation from unscheduled shutdowns can cost millions of Euros.
Networks of sensors could be used to monitor plant degradation so damaged parts can be scheduled for replacement long before they fail. Piezoelectric materials make excellent sensors, since they produce an electric current in response to movements, such as the pressure from a sound wave. Using these materials in installed sensors could determine the extent of degradation to the pipe and enable better maintenance scheduling.
However existing piezoelectric materials lose performance above 200 ºC, so when measuring hot surfaces, such as steam pipes, it is necessary to set them back from the pipe or use cooling techniques so reducing measurement accuracy. There is a need for new piezoelectric material that can operate effectively at higher temperatures, and better characterisation methods to demonstrate the viability of such materials for power plant sensing; an application where complete confidence is required before new technologies are embraced.
Solution
The EMRP Project Metrology of electrothermal coupling for new functional materials technology, evaluated many different new piezo-electric materials. One supplied by Leeds University, was shown to have great potential for high temperature measurements. This was further developed, tested and characterised in the project, demonstrating its suitability up to at least 380 ºC without losing performance. The characterisation demonstrated its viability both as a reference grade material and also for use in installed sensors that operate at high temperatures.
Impact
As a result of the project, IONIX, a company setup to commercialise these new piezoelectric materials, has had the materials properties confirmed by the project and now has the accurate data sheet needed to prove performance.
IONIX has developed these high temperature piezoelectric materials into a new line of ultrasonic sensors for use in extreme environments which extend beyond the capabilities of existing piezoelectric materials.
An accurate material property data sheet is vital for making the commercial case to sensor customers in power plants, where the introduction of new sensors requires the demonstration of 100% reliability. IONIX can now progress to the next step in sensor commercialisation; the extensive testing of prototypes needed to obtain a licence for use in power plants.
Once licensed, the sensor will be available for monitoring power plant integrity during operation. Improved operational sensing should save considerable costs by preventing unscheduled power plant shutdowns for repair as a result of failure. The sensors also have potential for use in other hostile environments such as oil wells, reducing reliance on manual inspections in hazardous locations to identify components that need changing.
- Category
- EMRP,
- New Technologies,