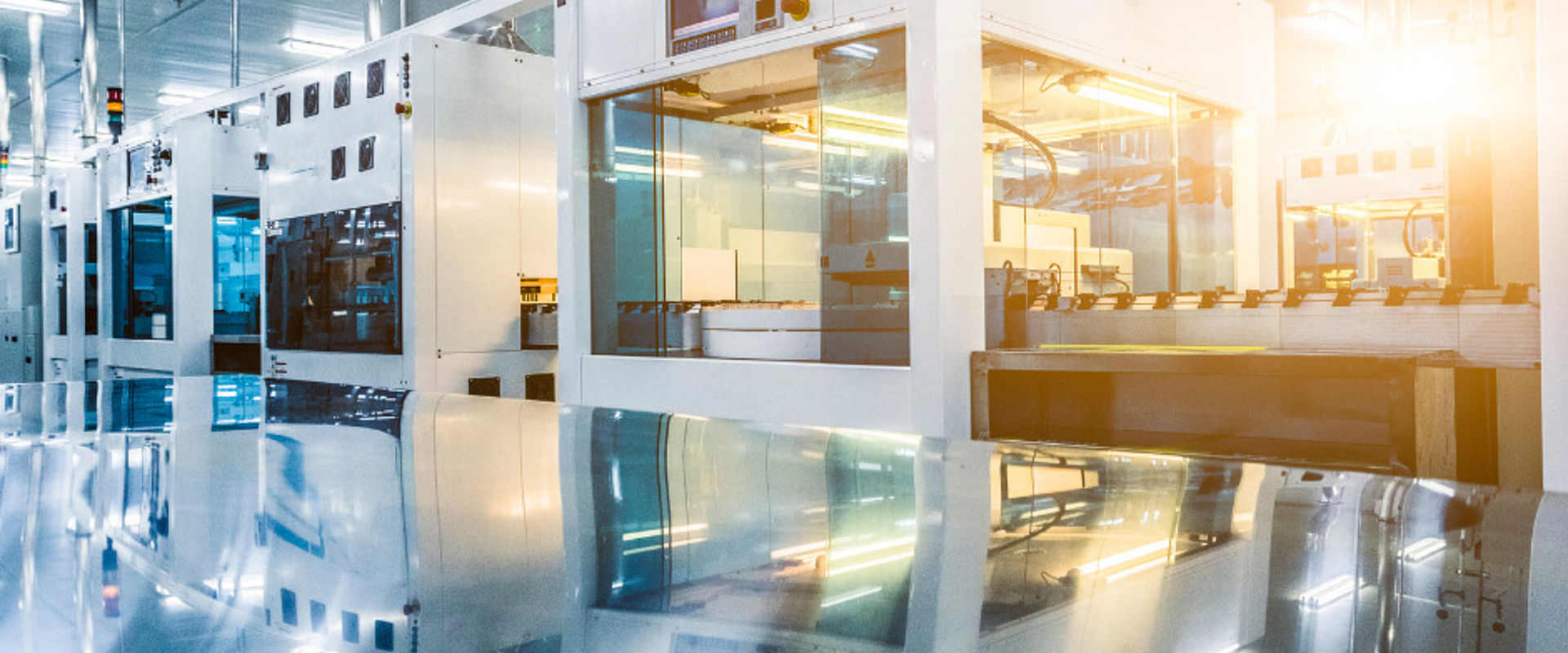
Modelling small surface features
Challenge
The semiconductor and optical industries create ever smaller components, whose functionality depends on sub-micron features. Highly accurate measurement methods are required in the production of photomasks - tools for depositing circuitry onto silicon wafers - as well as for measurements of the chips themselves.
Scatterometry, which illuminates a surface and detects the scattered light in reflections from it, could provide an ideal way to measure small structures in a production environment, but the time needed to process the data generated is hampering uptake.
Interpretation of light reflections requires fast, accurate, and rigorous modelling of the interactions between light and surface features. The current approach compares measurements to a library of pre-computed look-up tables, which is time consuming for the large data sets created by scatterometry.
Improved software is required to process these large and complex data sets in workable time frames. One method that offers potential is Finite Element Analysis (FEA), a mathematical technique which creates models of interactions at boundaries of complex geometries by subdividing them into simpler parts. FEA is used for predictive modelling of physical structures, and could be effectively applied to processing scatterometry data. Doing so will make measurements using scatterometry faster to run and easier to use.
Solution
The project Metrology of small structures for the manufacturing of electronic and optical devices, developed new models for processing scatterometric data to provide accurate measurement results of sub-micron 3D surface structures.
The project took extensive dimensional measurements of features on silicon wafers and photomasks using trusted scatterometry techniques in the optical to X-ray spectral range. This enabled the determination of errors, such as edge roughness, spot and structure size effects, which can all cause dimensional measurement inaccuracies. Using this data, mathematical models were created which can be used to evaluate and correct scatterometry measurements, including compensating for these effects. This approach enables fast, reliable 3D re-constructions of surface features from scatterometry measurements.
Impact
JCMwave, a developer of FEA software used in nano-optic design, carried out research as part of the project. In doing so, it was able to advance its FEA software for use in scatterometry measurements.
JCMwave evolved their existing FEA mathematical models to be suitable for use in scatterometric measurements, and developed its JCMsuite software to make it viable for this purpose. By comparing its FEA method to surface feature measurement and models developed by the project, JCMwave validated its own approach.
This independent validation gives JCMwave and its customer’s confidence in the use of JCMsuite, and FEA more generally for scatterometry measurements. Involvement in the project has helped the company gain new expertise in using FEA for processing optical measurement data, which has helped JCMwave improve its surface feature modelling capability.
As a result of software improvements, manufacturers of scatterometry instruments can ensure the accuracy of measurements of complex surface features and now have a method for handling the large data sets produced. This provides the electronics industry with a new technique for fast accurate surface measurements in a production environment, speeding the development of new, smaller electronics.
- Category
- EMRP,
- Industry,