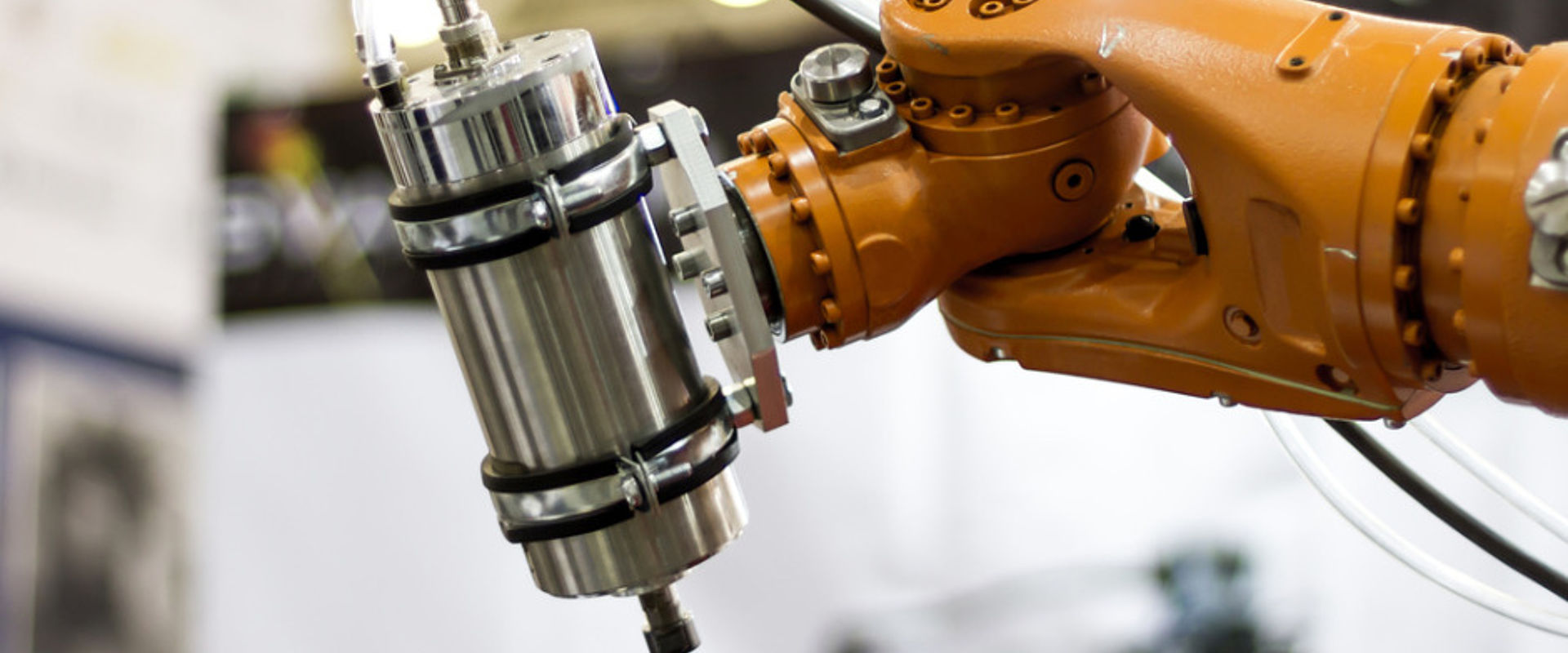
Nanoprecision positioning
Challenge
Precise positioning of miniature components during the manufacture of hard disk drives and the movement of robots during delicate medical surgery all rely on the exact positioning provided by linear drives. Nano-positioning devices are used in the manufacture of hard disk drives where exact positioning of components is essential for operation. These linear positioning drives are required to be small, compact, and fast with extremely accurate positioning to fulfil these operations. Similar precision is also needed for some advanced microscopy sample positioning stages and nano-measurement probes for example those used to measure wear experienced by nano-coatings increasingly used in high performance engineered products.
Linear positioning drives are at the heart of these delicate positioning movements. Manufacturing these is complicated involving many components produced using complex processes working at design limits. Improvements both to component design and simplification of the manufacturing process is required to increase positioning precision and enable greater accuracy in the measurement of ever smaller features.
Solution
National measurement institutes often make measurements that require very specialised instruments working at the boundaries of what is possible. In this case, the EMRP project Metrology to assess the durability and function of engineered surfaces required an improved positioning system for precise re-positioning of a nanomeasurement head over a test piece for repeat measurements of surface wear. Several prototypes of a positioning system based on optical interferometry were tested within the project, but meeting the exacting specification for the linear positioning drive using traditional manufacturing processes was difficult.
So TETRA GmbH Ilmenau, a developer of systems and components for sensors, robotics and automation, developed a novel optical sensor for the interferometers used in the project’s nanomeasurement instrument. To meet the exacting specifications, TETRA devised a new production method based on 3D printing and 5-axis machining technology. The resulting optical sensor is about the size of a sugar cube and capable of measuring metrescale distances with nanometre precision, making it ideal for use in many applications where small measurement errors and speed are important such as robotics and precision laser cutting.
Impact
This new sensor will be incorporated into TETRA’s high-end positioning systems, enabling a market-leading capability which has the potential to surpass the performance of other currentlyavailable positioning systems. TETRA estimate that several million Euro’s worth of business per annum could be generated from this novel new linear drive component when it is launched in 2017. The market for these positioning drives is expected to experience huge growth in coming years as other users in the semiconductor industry (global market worth $305 billion in 2013) and robotics industries (worth $32 billion in 2014) seek to benefit from improved positioning accuracy.
Increased positioning accuracy resulting from improvements to linear drives will enable a step-change in performance in many fields, such as the precise location of surgical tools used in eye-surgery, and the nano-positioning of micro-components becoming commonplace in manufacturing in the aerospace and automotive industries.
- Category
- EMRP,
- Industry,