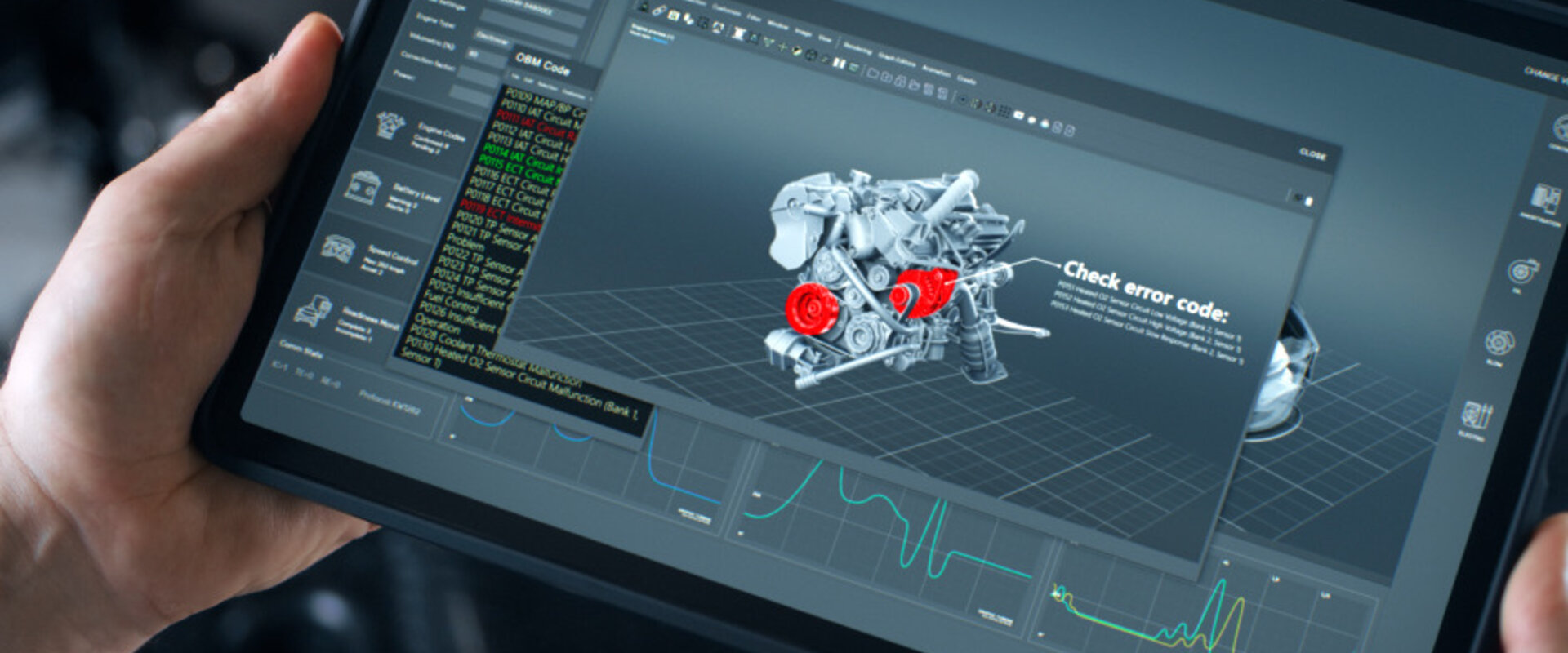
Providing accurate measurements for dynamic pressure applications
Challenge
Many industrial sectors involve processes that undergo dynamic changes in temperature and pressure. One key area is the automotive sector where around 99.8% of all global transport is powered by internal combustion engines (ICEs). It has been estimated that improvements in engine designs have the potential to reduce fuel consumption by 30%, representing a significant impact both on cost and the environment.
Correctly calibrating sensors for ICEs can improve fuel consumption, engine power and efficiency, but in these systems changes to both pressure, which can range from 60 - 300 bar in a few milliseconds, and temperature, which can reach 150oC, occur simultaneously. In industrial settings, pressure sensors are only calibrated with static standards that do not match the dynamic nature of ICE – leading to measurement errors of 10% or more. Whilst some dynamic pressure calibrators exist, these are mostly primary standards held by National Measurement Institutes (NMIs), which are time consuming and require a high level of expertise to use.
Easy, accurate, secondary dynamic calibration systems were needed to meet industry requirements of significantly improved accuracy and reliability of measurements, along with a better understanding of the influence of process conditions on sensor response.
Solution
During the DynPT project VTT MIKES, the NMI of Finland, and Testo Industrial Services designed and constructed a novel secondary pressure standard for dynamic calibrations.
A measurement chamber containing silicon oil optimized for calibrations over a large temperature range was connected to a movable piston, which in turn was connected to an actuator, driven by a waveform generator. Upon activation, the actuator allowed the piston to strike and compress the oil, generating pressure pulses ranging from 10 to 300 bar with a duration of around 1 ms.
Four outlets were added to the measurement chamber, one for a reference sensor and three to connect sensors under calibration. As commercial sensors are not standardised, adaptors were added to allow the attachment of different sensor thread types. Integrated heating elements were added to allow temperature measurements up to 200oC in a controlled manner.
Validation experiments demonstrated good reproducibility (<1%) with an expanded calibration uncertainty of about 2%. Traceability to the SI was realised by calibrating the reference sensor using VTT’s primary dynamic pressure standard.
Impact
Testo Industrial services GmbH is an ISO 17025 accredited company that calibrate measurement instruments for a wide range of European industries – including refrigeration, indoor climate monitoring, pharmaceuticals and automotive firms. The company’s participation in the DynPT project was motivated by their aim to provide dynamic pressure calibrations, that can provide measurements traceable to NMI’s and the SI, to a wider range of European Industries.
This has now been made possible with the new dynamic pressure calibrator. With a compact design and capable of temperature ranges and pressure pulses suitable for calibrating the piezoelectric pressure sensors for ICE applications, it can be used without the need for high expertise.
At the end of the DynPT project Testo and VTT continued to work together on the dynamic pressure calibrator, performing tests of various commercial static pressure sensors. This not only showed that many were not suitable to perform accurate measurements on dynamic systems, but also demonstrated where measurement errors arise – and how to correct for these.
Testo is now offering one of the first services for dynamic calibrations in Europe. Not only will such services lead to improvements in engine efficiencies, safety in areas such as ammunition and explosion testing, but also allow the development of new and improved dynamic sensors.
- Category
- EMPIR,
- Industry,
- EMN Advanced Manufacturing,